引言
钛合金因比强度高、耐腐蚀性好、热强度高等一系列优异的性能,在航空航天、国防工业等高端装备制造领域得到了广泛应用 [1] 。铣削是钛合金结构件加工中最常用的方法之一。但是,由于钛合金切削过程温度高、切削力大、刀具易磨损等,钛合金的加工表面质量很难控制 [2] 。探明钛合金铣削加工表面形貌特征及其对切削参数的响应规律,对实现钛合金加工表面质量调控和提升钛合金结构件服役性能具有重要理论和实践意义。
铣削加工表面形貌的创成取决于多种因素,如切削参数、刀具材料、刀具磨损程度等,其中切削工艺参数的优选是最直接和有效的方法 [3] 。目前,国内外众多学者对TC4钛合金铣削加工表面形貌及参数优化进行了一系列的研究。文献[4]对TC4钛合金进行了铣削加工,发现每齿进给量 f 对表面粗糙度 R a 的影响最 大 ,最 优 的 铣 削 参 数 组 合 为 :铣 削 速 度v c =100 m/min ,径 向 切 深 a e =4.3 mm ,每 齿 进 给 量f z =0.02 mm/齿 ,轴向切深 a p =0.05 mm ,可获得的表面粗糙度 R a =0.17 μm 。文献[5]通过开展侧铣实验,研究了不同切削速度 v c (48~108 m/min) 以及进给量f (0.04~0.06 mm/r) 下的TC4钛合金的表面粗糙度 R a 。
结果表明,在较高的切削速度和较低的进给量下,表面粗糙度降低了20%以上。文献[6]对TC4钛合金进行了不同切削速度 v c (30 mm/min和60 mm/min)和每齿进给量 f z (0.01 mm/齿和 0.05 mm/齿)的铣削实验,并分析了铣削表面粗糙度 S a 的变化规律。结果表明,f z 对 S a 的影响大于 v c ,较低的切削速度和进给速度可以获得较低的表面粗糙度,即较高的表面质量。
在切削工艺参数的优化方法研究方面,文献[7]基于遗传算法以磨损量、表面粗糙度和材料去除率为优化目标,对AISI 1040钢切削参数进行了多目标优化,获得了最优切削参数组合,预测误差在2%以下。文献[8]以铣削力和材料去除率为评价指标,采用粒子群优化算法对TC4钛合金加工参数进行了多目标优化,得 到 了 最 优 参 数 组 合 : v c =120 m/min , a e =1 mm ,f z =0.04 mm/z , a p =10 mm 。文献[9]以TC4钛合金铣削力和材料去除率为优化目标,基于遗传算法得到了加工参数的最优解集。文献[10]以铣削力、粗糙度、材料去除率建立了多目标优化模型,采用遗传算法求解获得了最优铣削参数解集,并通过实验证明了该方法的可行性。
为实现面向侧铣加工表面形貌的切削工艺参数优选,本文主要开展TC4钛合金侧铣加工实验研究。
从铣削加工表面微观缺陷、表面粗糙度随切削参数的响应规律和基于遗传算法的工艺参数优化3个方面进行研究,为TC4钛合金侧铣加工实践提供依据。
1、 TC4钛合金侧铣加工实验
试 验 材 料 为 TC4 钛 合 金 锻 坯 ,规 格 尺 寸 为30 mm×30 mm×5 mm 。材料微观组织结构和 EDS能谱如图1所示。
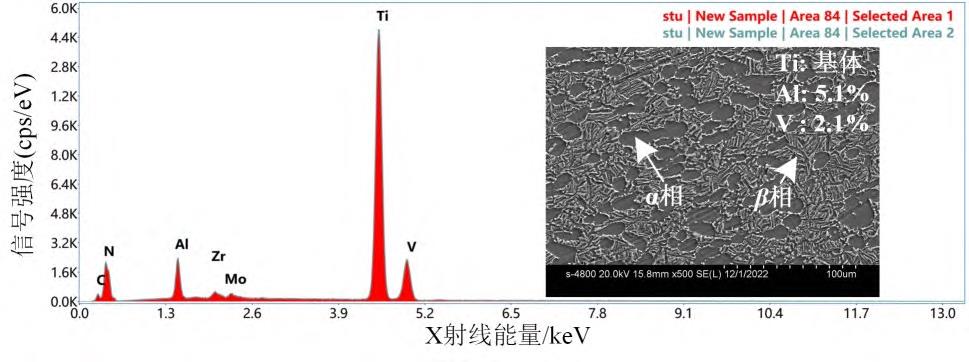
图1 TC4钛合金的微观结构和EDS能谱
Fig.1 Microstructure and EDS spectrum of TC4 titanium alloy
图中可以看出,TC4 钛合金是 α+β 型双相钛合金, α 相为基体相呈灰暗色, β 相为强化相附着在基体上,呈亮白色。TC4钛合金主要物理力学性能如表1所列。

侧铣加工实验在型号为GJ SEIKO LM-6050的数控机床上进行。加工刀具选用直径为50 mm的直角六齿可转位铣刀,刀片选用Kennametal公司生产的硬质合金 AlTiN(PVD)涂层刀片(APPT1135PESR-FSKC522M),其有效切削长度为11 mm。考虑到干切削方式可以避免切削液阻力引起的排屑不畅,保证加工精度的同时,可解决钛合金加工液冷成本高、污染环境等方面的问题。因此,实验加工方式选择干式铣削。侧铣加工实验现场如图2所示。
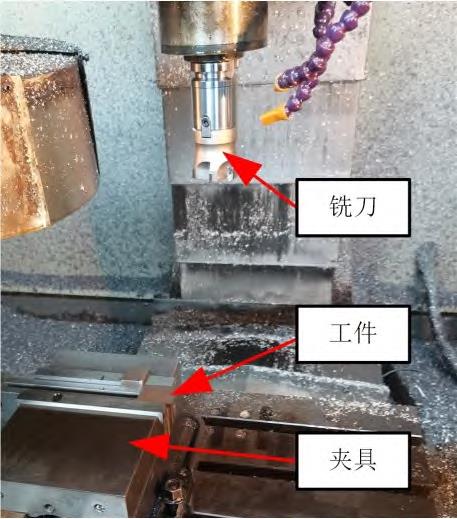
图2 铣削实验现场图
Fig.2 Field diagram of milling experiment
采用S-4800冷场发射扫描电子显微镜和基恩士形状测量激光显微系统 VK-X260K观测铣削后的表面形貌,测量三维表面粗糙度 S a 以及沿进给方向的二维表面粗糙度 R a 。
采用三因素四水平 L 16 (4 3 )正交实验方法开展实验,实验考察因素分别为主轴转速 n 、径向切深 a e 和每转进给量 f 。具体实验方案如表2所列。
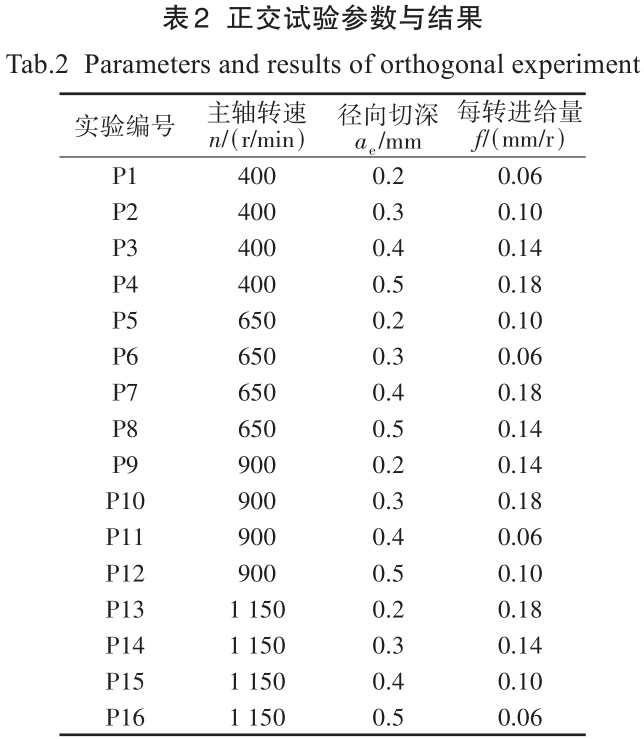
2 、结果与分析
2.1 加工表面缺陷
不同铣削条件下获得的加工表面形貌图及其对应的三维高度云图如图3所示。
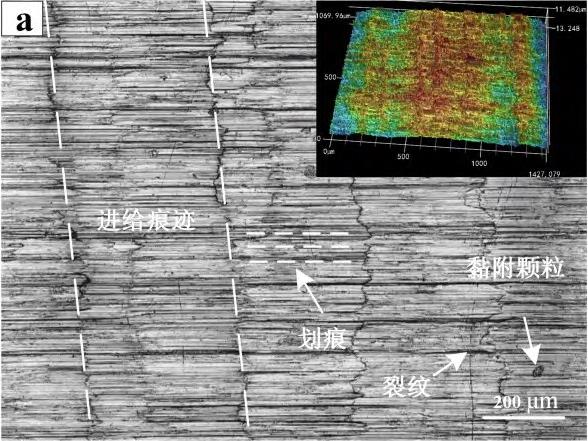
a) 编号P2
a) No. P2
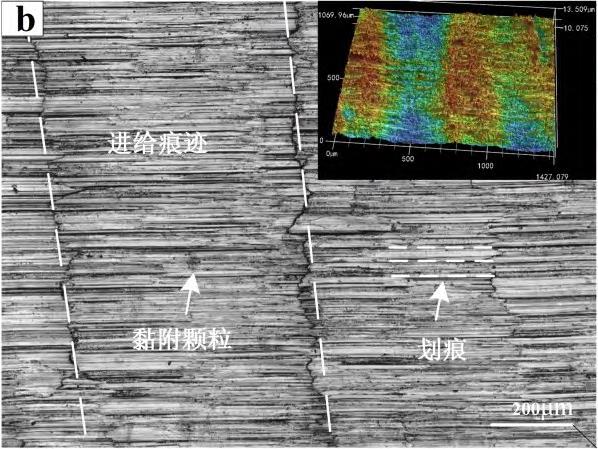
b) 编号P7
b) No. P7
图3 不同铣削参数下的表面形貌
Fig.3 Surface topographies under different milling parameters
从图3可以看出,加工表面呈现均匀分布的棱线,这是铣刀和工件之间相对运动所产生的进给痕迹,相邻进给痕迹之间的距离由进给速率决定。由于铣刀后角的影响,在相邻的进给痕迹之间产生了沿进给方向的划痕。进给刀痕和表面划痕可归结为侧铣加工表面固有缺陷,此类缺陷分布规律是由刀具几何特征和刀具-工件相对运动形成的。
此外,加工表面还观察到黏附颗粒、随机划痕和微小裂纹等缺陷。黏附颗粒可能是微小的切屑或者是从刀具上脱落的硬质点等 [11] 。对铣削表面的黏附颗粒进行能谱检测,检测结果如图4所示。图4 a)发现其成分与TC4钛合金基体材料基本相同。可以推断,黏附颗粒主要是在侧铣过程中高温的微切屑黏附到表面而形成。表面上还存在一些随机方向的划痕,这是从铣刀上剥落的硬质点、积屑瘤或者切屑在铣削表面滑擦产生 [12-13] 。图4 b)中,划痕的能谱分析结果与TC4钛合金的基体材料基本相同。可以推断,随机无定向划痕是由积屑瘤或碎屑在刀具和工件之间的接触面滑擦形成。此外,在干式铣削的条件下,由于加工区域中存在较高的热应力和机械应力,铣削表面便产生了微小裂纹 [14] 。
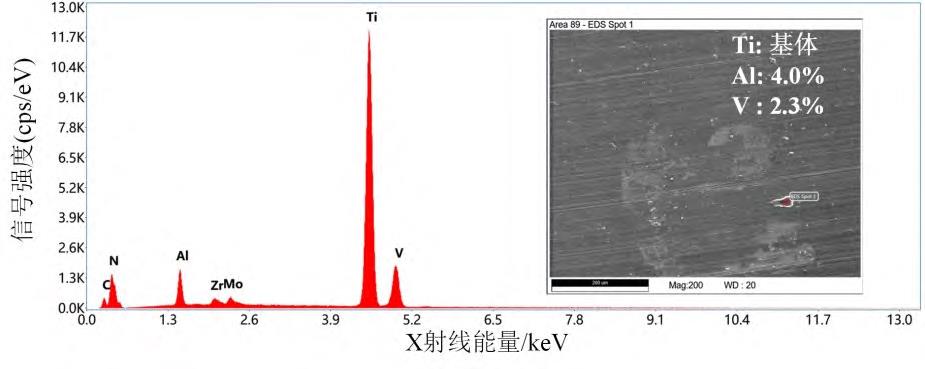
a) 黏附颗粒
a) adhesive particle
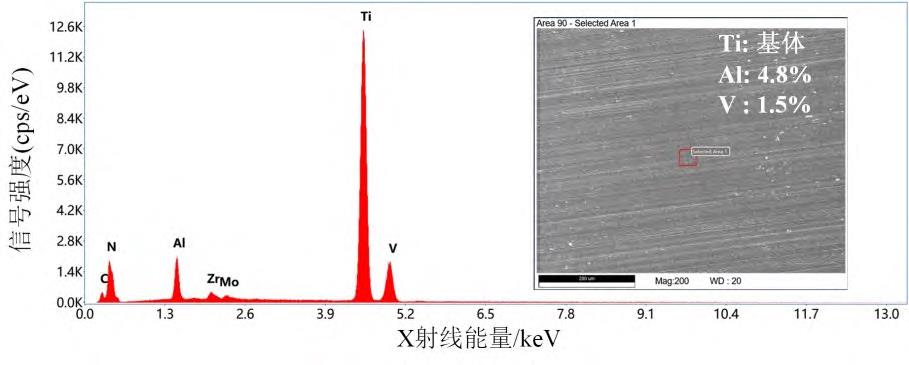
b) 划痕
b) scratch
图4 侧铣表面缺陷的EDS能谱
Fig.4 EDS spectrum of surface defects in peripheral milling
2.2 铣削表面粗糙度
不同铣削工艺条件下,加工表面粗糙度 R a 和 S a 随切削工艺参数的响应规律如图5所示。
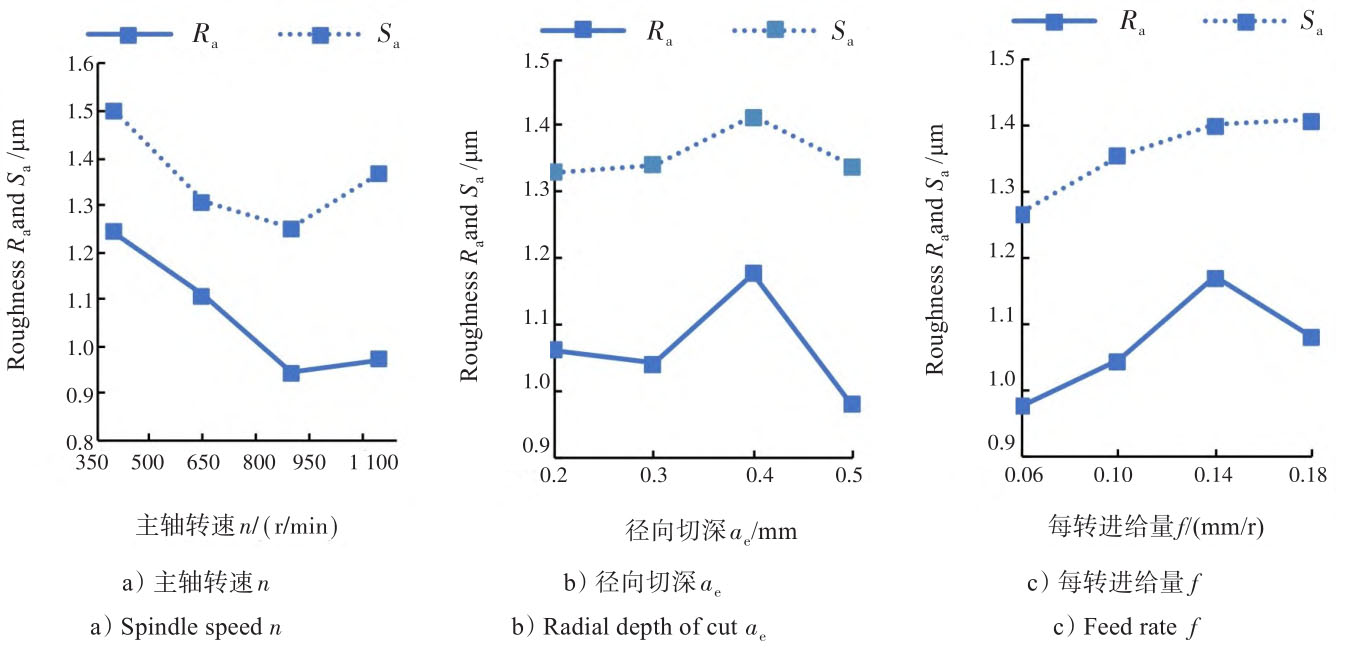
图5 不同铣削参数对表面粗糙度 R a 和 S a 的影响
Fig.5 Effect of different milling parameters on surface roughness R a and S a
图5 a)中,表面粗糙度 R a 的值随着主轴转速 n 从400 r/min 增加到 900 r/min 而减小,并在 n=900 r/min时达到最小值( R a =0.944 μm )。当主轴转速超过900 r/min 时,表面粗糙度呈上升趋势。主轴速度的增加意味着材料变形率的增加,这将导致在铣削过程中产生更多的热量。铣刀和工件接触表面之间的热量积累会软化TC4钛合金材料,材料的塑性流动使得铣削后的表面粗糙度有所降低 [15] 。但当主轴速度继续增加时,刀具与工件接触表面上积聚的热量将难以快速消散,导致切屑与铣刀、加工表面间的黏附力增加,从而增加了铣削力 [16] 。此外,在较高的主轴转速下,应变硬化和应变率硬化对铣削力的影响大于热软化,这也导致铣削力呈上升趋势 [17] 。铣削力的增加会使刀具产生颤振现象 [18] ,影响了加工的精度,从而恶化了铣削表面质量,导致表面粗糙度的增加。
图6为主轴转速 900 r/min 和 1 150 r/min 下观测的加工表面形貌图。可以看出,随着主轴转速的增加,铣削表面质量降低。在 n=1150 r/min 时获得的表面高度波动远大于在 n=900 r/min 处获得的表面高波动,并且表面上黏附颗粒数量大于在 n=900 r/min 下获得的。
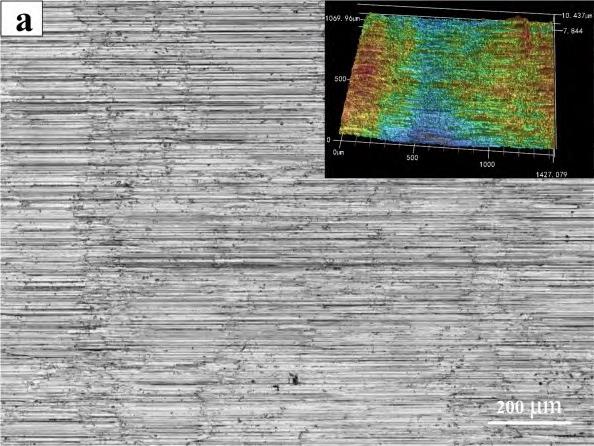
a) 编号P11
a) No. P11
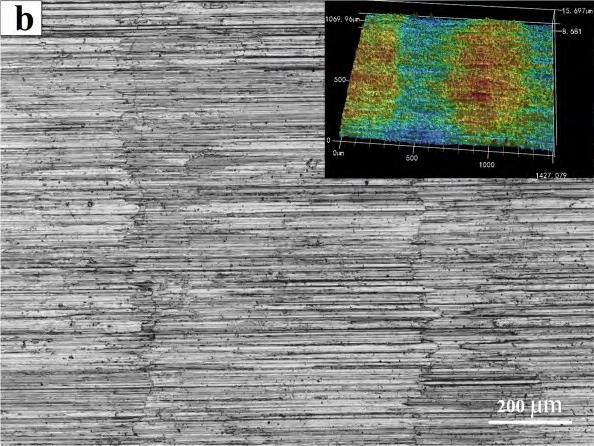
b) 编号P16
b) No. P16
图6 在不同主轴转速下的铣削表面形貌
Fig.6 Milling surface topography at different spindle speeds
在图 5 b)中,随着径向切深 a e 由 0.2 mm 增加到0.4 mm,表面粗糙度 R a 的值先是减小了 1.88%,然后显著增加。一方面,工件在加工之前进行了预加工以找平加工面。铣刀和工件表面之间的挤压和摩擦会导致表面纤维化,从而硬化了待加工表面 [19-20] 。另一方面,TC4钛合金的化学活性非常高,很容易与空气中的元素反应,产生表面硬化层,这也导致了表面硬度的增加 [21] 。因此,适当增加径向切削深度会使铣刀在一定程度上避免产生表面硬化层,从而更容易切削材料,使表面粗糙度值略微下降。但铣削过程中,材料剪切区的横截面积会随着径向切深的增加而增加,并且单位时间材料去除率的增加将导致铣削力的增加,从而使表面粗糙度增加。图7为径向切深0.3 mm和0.4 mm下观测的加工表面三维形貌图,径向切深的增加导致表面上黏附颗粒、划痕的增加和表面质量的恶化。当径向切深 a e 超过0.4 mm时,表面粗糙度呈下降趋势。这可解释为挤压变形的进一步增加使铣削温度升高,表面热软化效应变得显著 [22] 。因此,表面材料更容易去除,并且表面质量得到改善。

a) 编号P14
a) No. P14
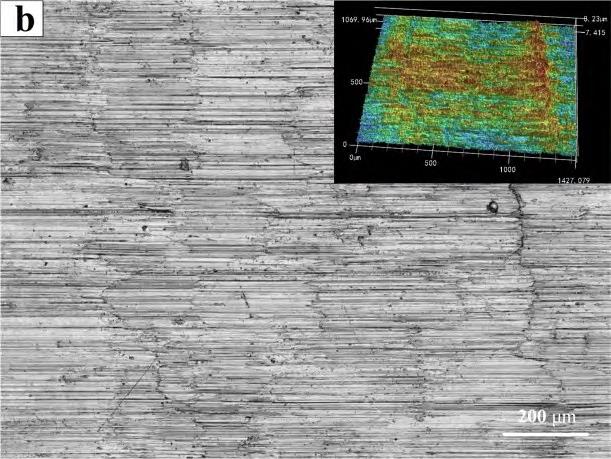
b) 编号P15
b) No. P15
图7 不同径向切深下的铣削表面形貌
Fig.7 Milling surface topography at different radial depth of cut
在图 5 c)中,随着进给量 f 从 0.06 mm/r 增加到0.14 mm/r,表面粗糙度 R a 的值增大了19.9%。这是由于铣刀在进给方向上每单位切削面积的切削时间减少,加工表面上相邻峰和谷之间的间距和形态差异增加。铣刀在加工表面上的残余高度也有所增加,最终导致表面粗糙度增加。特别是在图3中,进给痕迹间的不均匀间距会恶化表面质量,这可归因于铣削力的增加使铣刀在加工过程中产生了振动 [23] 。当进给量 f超过 0.14 mm/r 时,表面粗糙度 R a 呈现减小的趋势。这可归因为铣削温度变高软化了TC4钛合金材料 [24] ,从而使材料更容易去除,表面粗糙度降低。另一种可能是涂抹效应 [25] ,效应降低了工件表面峰值的高度,从而使表面粗糙度 R a 降低。较高的机械载荷和热载荷促使了这种现象的发生。图8为进给量0.14 mm/r和0.18 mm/r下观测的加工表面三维形貌。随着进给量的增加,铣削表面上后刀面引起的划痕变得更加清晰均匀,表明表面质量有所改善。
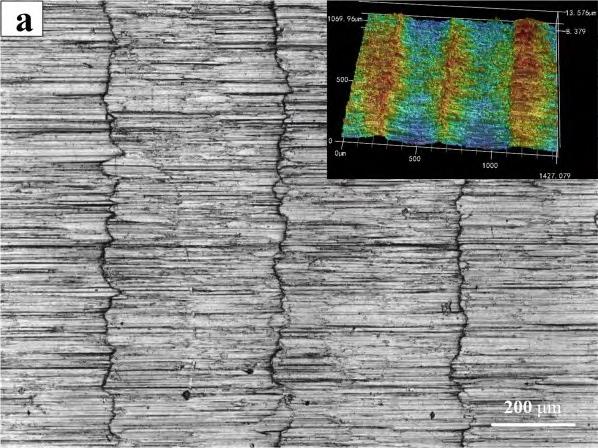
a) 编号P3
a) No. P3
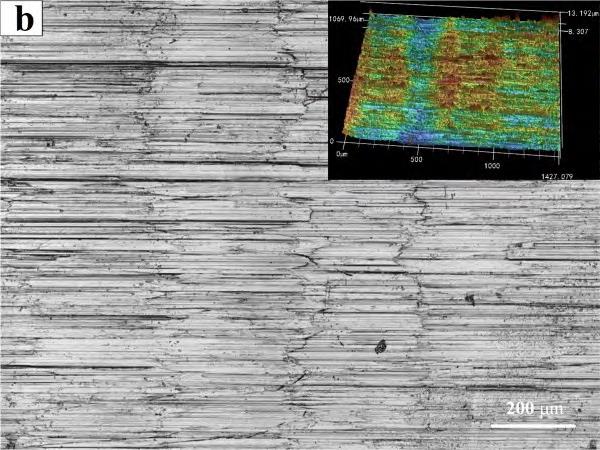
b) 编号P4
b) No. P4
图8 不同进给量下的铣削表面形貌
Fig.8 Milling surface topography at different feed rate
从图5还可以看出,粗糙度 S a 的值都高于沿进给方向的粗糙度 R a , S a 与 R a 随铣削参数有类似的变化趋势,但并不完全相同。图5 a)中,表面粗糙度 S a 随主轴转速具有先降低后增加的相同趋势,并在 n=900 r/min时达到最小值( S a =1.250 μm );图5 b)中,随着径向切深 a e 由 0.2 mm 增加到 0.3 mm,粗糙度 S a 增大了0.75%,这与粗糙度 R a 的变化趋势恰恰相反;图 5 c)中,当进给量 f 超过0.14 mm/r时,粗糙度 S a 的值反而呈上升趋势,这是因为TC4钛合金侧铣表面不仅包含沿着进给方向的表面特征,还包括垂直于进给方向的特征,如划痕、随机颗粒等。特别是铣刀后角引起的划痕,其在垂直于进给方向的高度波动导致表面粗糙度 S a 的增大。
3 、基于遗传算法的侧铣工艺参数优化
遗传算法(Genetic Algorithm,GA)是 1 种模拟达尔文进化论中自然选择和遗传学机理生物进化过程的计算模型。该算法将问题求解的过程转换成生物体中染色体选择、交叉和变异的过程,相对于一些常规优化算法,其计算简单高效。算法的基本流程如图9所示。
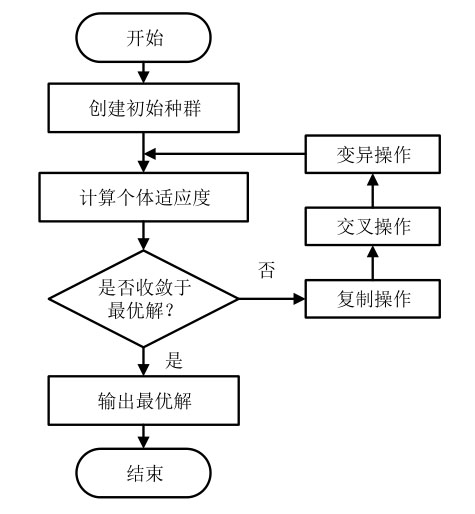
图9 遗传算法基本流程图
Fig.9 Basic flowchart of genetic algorithm
将主轴转速 n 、径向切深 a e 、每转进给量 f 作为优化模型的变量,根据正交试验结果以及各铣削参数的取值范围,可以得到优化目标的约束方程如下:

则优化的数学模型可写为:

借助MATLAB数学软件平台,采用Gamultiobj函数进行优化问题的求解。在 Gamultiobj函数的参数中,交叉概率和变异概率的选择对种群的更新影响最大。交叉的概率过低会大大降低种群的更新速度,交叉概率过高会破坏种群内的最优解;变异概率过低会使种群内的有效基因缺失,变异概率过高虽使得种群多样性增大,但会使现有种群规模遭到破坏。因此,需要根据实际求解问题,对参数进行合理的处理,具体参数设置如表3所示。
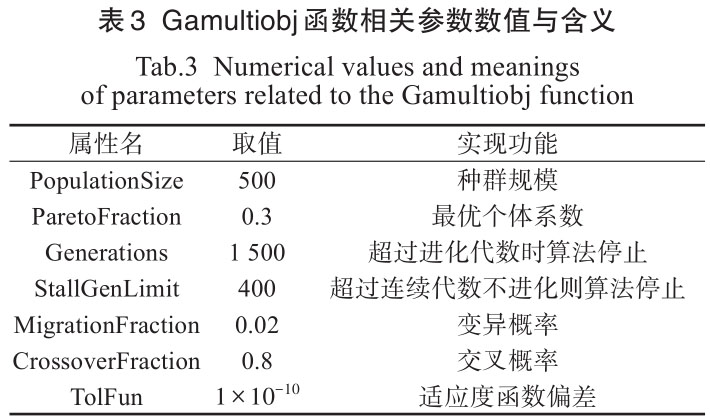
求解后,获得了150组帕累托(Pareto)最优解,对应的粗糙度值如图10所示,部分最优解如表4所示。
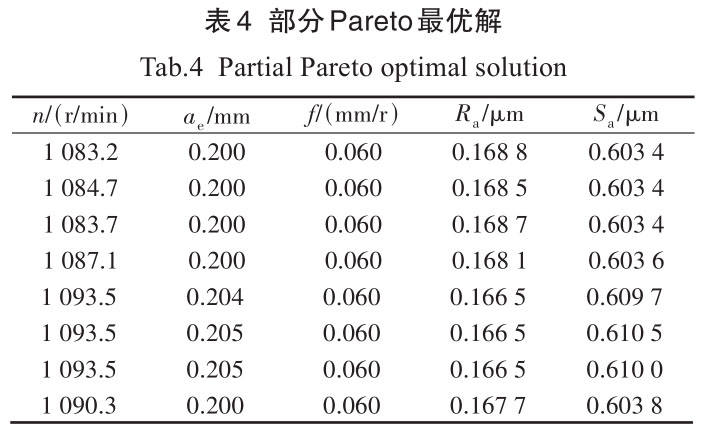
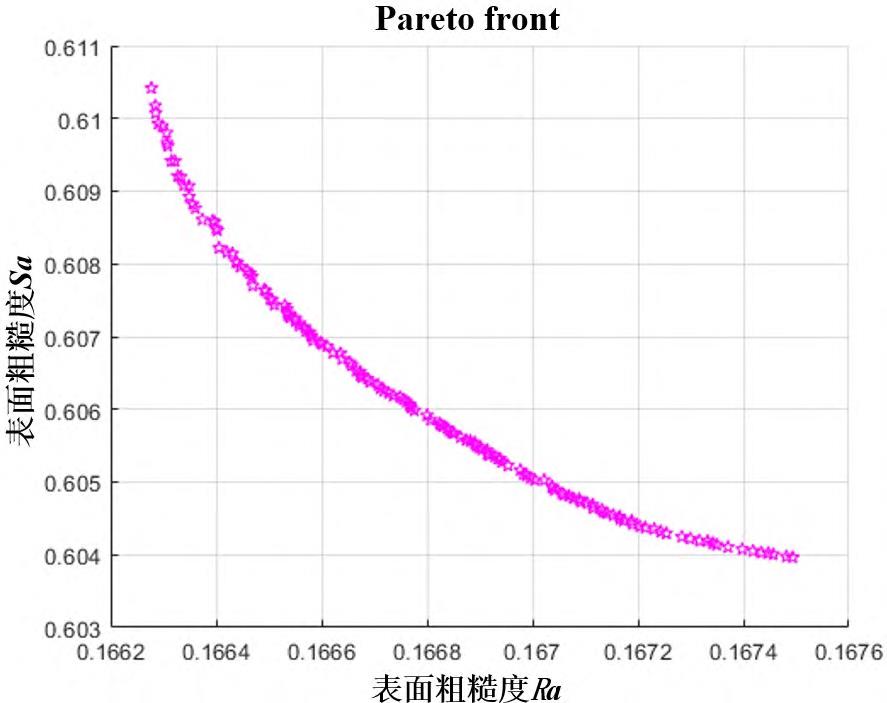
图10 Pareto前端解集
Fig.10 Pareto front set
采用隶属度函数对Pareto解集中的最优解进行评价:

式(4)中: f i 表示第 i 个目标函数, i=1,2 ;最优结果选取P 值最大时对应的Pareto解集中的铣削参数。
最终得到的多目标优化结果为
x= ( ) 1 093.48,0.201,0.060
T ,根据实际加工经验对结果进行近似处理后得到的加工参数为:主轴转速n=1093 r/min ,径向切深 a e =0.2 mm ,每转进给量f=0.06 mm/r ,对应的目标粗糙度值为 R a =0.167 3 μm 和S a =0.604 3 μm 。
4、 结论
1) TC4钛合金侧铣加工表面微观缺陷主要包括进给刀痕、后刀面摩擦划痕、黏附颗粒、微小裂纹和随机划痕等。进给刀痕和后刀面摩擦划痕可归结为侧铣加工表面固有缺陷,此类缺陷分布规律是由刀具几何特征和刀具-工件相对运动形成的;黏附颗粒、随机划痕和微小裂纹等随机性缺陷,主要是微小切屑附着、积屑瘤摩擦以及在热应力和机械应力的作用下产生的。
2) 铣削表面粗糙度随主轴转速的增大先减小后增大;随径向切深的增大先增大后减小;随进给量先增大后减小。但 R a 和 S a 随铣削参数的变化规律并不完全,这是因为铣削表面不仅包含沿进给方向的特征,还包括垂直于进给方向的特征,特别是铣削后角引起的划痕,其在垂直于进给方向的高度波动使得 S a数值增大。
3) 基于遗传算法以最小表面粗糙度值为优化目标,在实验参数范围内得到的最优侧铣参数组合为:
主轴转速 n=1 093 r/min ,径向切深 a e =0.2 mm ,每转进给量 f=0.06 mm/r 。在该条件下,可获得较小的表面粗糙度值,即 R a =0.167 3 μm 和 S a =0.604 3 μm 。
参考文献:
[1] HOURMAND M, SARHAN A A D, SAYUTI M, et al. A comprehensive review on machining of titanium alloys [J]. Arabian Journal for Science and Engineering, 2021,46(8): 7087-7123.
[2] PASCHOALINOTO N W, BATALHA G F, BORDINAS‐SI E C, et al. MQL strategies applied in Ti-6Al-4V alloy milling-comparative analysis between experimental de‐sign and artificial neural networks[J]. Materials, 2020, 13(17): 3828.
[3] YAN BOLING, ZHU LIDA, LIU CHANGFU. Prediction model of peripheral milling surface geometry considering cutting force and vibration[J]. The International Journalof Advanced Manufacturing Technology, 2020, 110(5):1429-1443.
[4] 纪煦, 朱玮瑜, 付宏鸽, 等. 基于曲面响应法的TC4铣削加工表面粗糙度研究[J]. 北华航天工业学院学报,2022, 32(4): 11-13, 20.
JI XU, ZHU WEIYU, FU HONGGE, et al. Surface roughness of TC4 milling based on surface response method[J]. Journal of North China Institute of Aerospace Engineering, 2022, 32(4): 11-13, 20. (in Chinese)
[5] SUR G, MOTORCU A R, NOHUTÇU S. Single and multi-objective optimization for cutting force and surface roughness in peripheral milling of Ti6Al4V using fixed and variable helix angle tools[J]. Journal of Manufactur‐ing Processes, 2022, 80: 529-545.
[6] LIZZUL L, SORGATO M, BERTOLINI R, et al. Anisot‐ropy effect of additively manufactured Ti6Al4V titanium alloy on surface quality after milling[J]. Precision Engi‐neering, 2021, 67: 301-310.
[7] VUKELIC D, SIMUNOVIC K, KANOVIC Z, et al.Multi-objective optimization of steel AISI 1040 dry turn‐ing using genetic algorithm[J]. Neural Computing and Ap‐plications, 2021, 33(19): 12445-12475.
[8] 巩亚东, 丁明祥, 李响, 等. TC4钛合金材料铣削加工分析及参数优化[J/OL]. 吉林大学学报(工学版): 1-10(2022-11-09) [2023-10-12]. https://doi. org/10.13229/j.cnki.jdxbgxb20220681.
GONG YADONG, DING MINGXIANG, LI XIANG, et al. Milling analysis and parameters optimization for TC4 titanium alloy material[J/OL]. Journal of Jilin University:Engineering and Technology Edition: 1-10(2022-11-09)[2023-10-12]. https://doi. org/10.13229/j. cnki. jdxb‐gxb20220681. (in Chinese)
[9] 李体仁, 胡晓强. 高速铣削钛合金TC4切削力试验研究及切削参数优化[J]. 机床与液压, 2019, 47(1): 45-48.
LI TIREN, HU XIAOQIANG. Experimental research on cutting force of high speed milling titanium alloy TC4 and optimization of cutting parameters[J]. Machine Tool & Hydraulics, 2019, 47(1): 45-48. (in Chinese)
[10] 鲍骏, 白海清, 任礼, 等. TC4钛合金铣削性能分析及多目 标 参 数 优 化 [J]. 科 学 技 术 与 工 程 , 2021, 21(36):15400-15410.
BAO JUN, BAI HAIQING, REN LI, et al. Analysis of milling performance of TC4 titanium alloy and optimiza‐tion of multi-objective parameters[J]. Science Technology and Engineering, 2021, 21(36): 15400-15410. (in Chi‐nese)
[11] ULUTAN D, OZEL T. Machining induced surface integri‐ty in titanium and nickel alloys: a review[J]. International Journal of Machine Tools and Manufacture, 2011, 51(3):250-280.
[12] GINTING A, NOUARI M. Surface integrity of dry ma‐chined titanium alloys[J]. International Journal of Ma‐chine Tools and Manufacture, 2009, 49(3/4): 325-332.
[13] LIANG XIAOLIANG, LIU ZHANQIANG, WANGBING. State-of-the-art of surface integrity induced by tool wear effects in machining process of titanium and nickel alloys: a review[J]. Measurement, 2019, 132: 150-181.
[14] MASOUDI S, ESFAHANI M J, JAFARIAN F, et al.Comparison the effect of MQL, wet and dry turning onsurface topography, cylindricity tolerance and sustainabil‐ity[J]. International Journal of Precision Engineering and Manufacturing-Green Technology, 2023, 10(1): 9-21.
[15] CARVALHO S, HOROVISTIZ A, DAVIM J P. Surface topography in machining Ti alloys for biomedical applica‐tions: correlative microscopy approach for qualitative and quantitative analysis[J]. The International Journal of Ad‐vanced Manufacturing Technology, 2021, 114(3): 683-694.
[16] KE YINGLIN, DONG HUIYUE, LIU GANG, et al. Use of nitrogen gas in high-speed milling of Ti-6Al-4V[J]. Transactions of Nonferrous Metals Society of China,2009, 19(3): 530-534.
[17] ULLAH I, ZHANG SONG, ZHANG QING, et al. Micro‐structural and mechanical property investigation of ma‐chined surface layer in high-speed milling of Ti-6Al-4V alloy[J]. The International Journal of Advanced Manufac‐turing Technology, 2021, 116(5): 1707-1719.
[18] LUO MING, YAO QI. Vibrations of flat-end cutter enter‐ing workpiece process: modeling, simulations, and experi‐ments[J]. Shock and Vibration, 2018, 2018: 8419013.
[19] CHEN ZHEN, HUANG CHUANZHEN, LI BINGHAO,et al. Experimental study on surface integrity of Inconel 690 milled by coated carbide inserts[J]. The InternationalJournal of Advanced Manufacturing Technology, 2022,121(5): 3025-3042.
[20] SONG WENGANG, LIU ZHANQIANG, YAO GONG‐HOU, et al. Effect of workpiece work hardening on ma‐chined surface topography generated in two-step milling process[J]. Journal of Manufacturing Processes, 2022, 77:348-360.
[21] GULERYUZ H, CIMENOGLU H. Oxidation of Ti–6Al–4V alloy[J]. Journal of Alloys and Compounds, 2009,472(1/2): 241-246.
[22] 杜舜尧. 新型钛合金加工表面完整性与疲劳性能研究[D]. 南京: 南京航空航天大学, 2017.
DU SHUNYAO. Research on surface integrity and fa‐tigue property in machining of new titanium alloy[D].Nanjing: Nanjing University of Aeronautics and Astronau‐tics, 2017. (in Chinese)
[23] ZHU SIYUAN, ZHAO MAN, MAO JIAN, et al. A Ti-6Al-4V milling force prediction model based on the tay‐lor factor model and microstructure evolution of the mill‐ing surface[J]. Micromachines, 2022, 13(10): 1618.
[24] WANG TAO, LI YANG, LIU JIAQI, et al. Milling force and surface topography of Ti-6Al-4V titanium alloy clad‐ded by the laser[J]. Surface Review and Letters, 2019, 26(5): 1850185.
[25] GUTZEIT K, BULUN G, STELZER G, et al. Sub-zero milling of Ti-6Al-4V—impact of the cutting parameters on the resulting forces, tool wear, and surface quality[J].The International Journal of Advanced Manufacturing Technology, 2023, 126(7): 3367-3381.
相关链接