1、 引言
为了解不同的轧制工艺对TC11钛合金厚板组织和性能的影响,本章着重从轧制温度、轧制变形量、轧制换向方式三方面入手对TC11钛合金厚板的组织与性能开展研究。分析不同的开坯轧制温度、轧制变形量和轧制换向方式对 TC11钛合金厚板热态以及退火态组织性能的影响,确定最佳的轧制工艺参数。本文章采用四辊可逆式 1200mm 热轧机参数如表 3.1 所示。

2 、开坯温度对TC11钛合金厚板组织及性能影响
为了研究不同的轧制温度对TC11钛合金厚板组织和性能的影响,本文采用了两种不同的轧制温度对TC11板材进行开坯轧制[57],表 3.2 为不同轧制温度的轧制工艺。
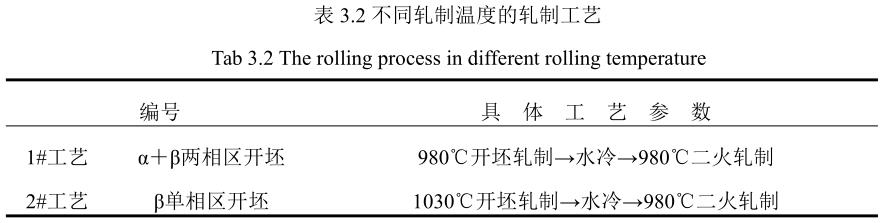
对两种不同的开坯工艺制得的 40mm 厚TC11板材,分别测试其热态的显微组织及力学性能,并进行对比,研究不同的轧制温度对TC11厚板热态显微组织的影响,随后对两种工艺下制得的板材进行 990℃/1h AC+550℃/6h FC 成品热处理,对比分析两种工艺对成品TC11板材的组织及性能的影响。
2.1 开坯温度对TC11钛合金厚板显微组织的影响
为研究不同的轧制温度对TC11钛合金厚板热态显微组织的影响,对不同轧制温度的工艺下制得的热态板材显微组织进行了观察。图 3.1 为经两种不同开坯轧制温度制得 40mm 厚热轧板的显微组织。
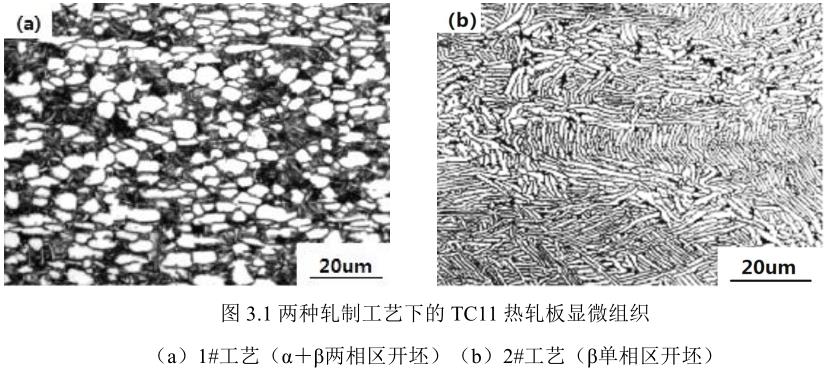
从图中我们不难看出,不同的开坯温度对TC11钛板材的热态显微组织影响很大。板材经 1#工艺(α+β两相区开坯)轧制后获得了α+β两相区加工组织,板材的显微组织由等轴的初生α和片层状的次生α以及β相组成。这是由于在该工艺下,板材两火轧制均在两相区上部开始变形,并终止在两相区,在变形的过程中发生动态回复与再结晶。经变形后,初生α等轴化,同时,在冷却的过程中β基体上逐渐析出片层状的次生α,从而板材获得了典型的双态组织,该组织的综合力学性能较好。而板材经过 2#工艺(β单相区开坯)轧制后虽然也获得了α+β两相区加工组织,但组织形貌与 1#工艺截然不同,板材的显微组织由细小的网篮组织组成。
这是由于在该工艺下,板材在β单相区开坯轧制,即板材在单相区开始变形,变形终止在两相区。随着轧制的温降,在β晶界处优先析出α相,因此晶界α最早承受变形,随着变形的进一步增加,长条的晶界α断开,形成断续的α相,而晶粒内部析出的α束集经过一定的变形相互交错,形成编织状。该类型组织有利于阻碍裂纹扩展,提高板材的断裂韧性和冲击韧性[65]。
对两种轧制工艺下获得的热态板材进行热处理,热处理制度为 990℃/1hAC+550℃/6h FC,对其显微组织进行了观察。图 3.2 为经两种不同开坯轧制温度,两火轧至 40mm 后,经 990℃/1h AC+550℃/6hFC 双重退火后的显微组织。
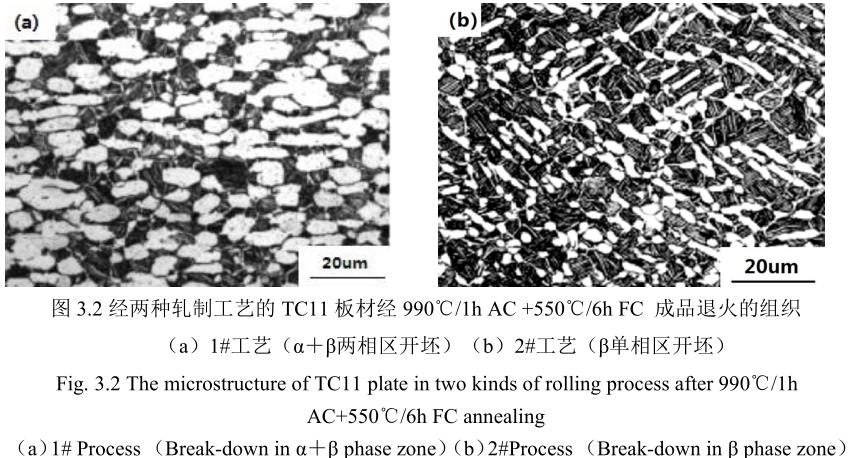
从图中我们可以看出,两种工艺下的板材经成品退火后,初生α晶粒逐渐等轴化,次生α晶粒条状化,呈双态组织。但也有明显区别,1#板材经退火后,初生α晶粒在有着明显长大,经检测,其平均晶粒尺寸为 10~20μm,而 2#板材经高温退火后,α相向β相转变,且编织状的长条α逐渐等轴化,在后续时效过程中,β基体中析出次生α,呈条状分布,初生α晶粒尺寸较 1#工艺板材细小,约 10μm 左右。
2.2 开坯温度对TC11钛合金厚板性能的影响
为研究不同的轧制温度对TC11钛合金厚板性能的影响,对不同轧制温度的工艺下制得的热态板材的纵、横向室温拉伸和冲击性能进行了测试。表 3.3 为经两种不同开坯轧制温度轧至 40mm 时热轧板的纵、横向力学性能。

由上表我们不难看出,1#与 2#工艺下板材的纵横向力学性能差异均较小,并且 1#工艺的室温抗拉强度略高于 2#工艺的板材,且延伸率与断面收缩率明显优于2#工艺的板材,但冲击性能明显低于 2#工艺的板材。这是由于开坯温度不同导致的板材组织不同。一般情况下网篮组织的抗拉强度与冲击性能优于等轴组织,而延伸率偏低。但是优于动态回复与再结晶的作用,1#工艺在β基体中存在一定量的片层状次生α’相。次生α’相一定程度上提升了板材的抗拉强度,但是由于次生α’相过于薄并且体积分数较低,因此对冲击性能改善不明显。
对两种轧制工艺下获得的热态板材进行热处理,热处理制度为 990℃/1hAC+550℃/6h FC,对其纵、横向室温拉伸和冲击性能进行了测试。表 3.4 为经两种不同开坯轧制温度,两火轧至 40mm 后,经 990℃/1h AC+550℃/6h FC 双重退火后的力学性能。
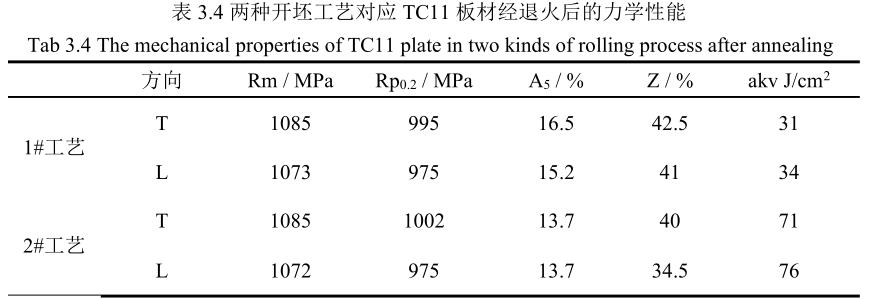
从上表可以看出,经 990℃/1h AC+550℃/6h FC 双重退火后,两种工艺板材纵横向力学性能均较好,较退火前 1#、2#工艺的板材抗拉性能有小幅度提升,1#工艺的延伸率以及 2#工艺的冲击性能有大幅度提升。1#工艺是由于球状的亚稳定β相继续分解,同时片层状的次生α’相逐渐增厚,并且初生α相继续长大所致。而2#工艺的拉长的初生α相逐渐断裂,然后长大。同时次生α’在拉长的β晶界处生成,因原始的初生α相呈编织状排列。由于组织的继承性,退火后的组织也沿原始β晶界程一定编织状排列,因此极大的提高了材料的冲击性能。
因此,综合考虑 1#、2#工艺的热态和退火态的组织和力学性能以及最终不同状态TC11成品的需求量,对于退火态板材供货的产品采用 1#工艺进行生产,对于热态交货的产品采用 2#工艺生产。
3、轧制方式对TC11钛合金厚板组织及性能影响
由于供货激光成型用基板的TC11厚板要求网篮组织供货,而普通TC11厚板要求双态组织供货。编织状态的TC11厚板与双态组织供货的TC11厚板均与原始组织编制状态有关。由于同一锭号的板坯数量有限,为产品交付后的稳定性同时节约材料,本章节只采用 2#工艺的板材进行轧制方式的比对热轧方式对材料纵横向力学性能差异的影响。轧制方式确定前对板坯坐标系加以定义,如图 3.3 所示,方便后文描述。

板材的热轧方式主要有以下五类:
(1)全纵轧法。所谓纵轧就是板材的延伸方向与原料(板坯)纵轴(Y 轴)方向相一致的轧制方法。
(2)全横轧法,即将板坯进行横轧(沿 X 轴)直至轧成成品。此法只能用于板坯长度大于或等于成品板材宽度时。
(3)综合轧制法即横轧—纵轧法。综合轧制法,一般分为三步,首先纵轧(沿Y 轴)1~2 道次,平整板坯,称为成型轧制,然后转 90°(沿 X 轴)延伸到所需的板宽,称为展宽轧制。然后再转 90°(沿 Y 轴)进行纵轧成材,称为延伸轧制。
(4)角轧—纵轧法。所谓角轧就是将轧件纵轴与轧辊轴线成一定角度(与 Y轴成一定角度)送入轧辊进行轧制的方法。
(5)纵横轧制法。即先沿板坯的纵轴(Y 轴)轧制较大的变形量到一定程度,通过剪切下料的方式垂直于开坯轧制方向切出板材宽度,再换向 90°进行以后的轧制的方法。
就这五类轧制法进行分析,(4)由于采用一定角度换向,几何损失大,批次稳定性控制难度大,在现代工厂轧制中已经很少用到,一般在轧制宽幅较大的板材过程中,如出现板材延长度方向上的不均匀形变,或者来板坯厚度较大时,在轧制过程道次中间选择采用,本研究中不考虑。
(1)~(2)都是始终沿着一个方向轧制,各向异性必然最大,成品板材纵向变形量最大,因此纵向一般情况下优于横向。本章节将(1)、(2)合并,考虑为一种轧制方式。(3)、(5)由于存在纵、横两个方向的变形,考虑到成品板材厚度 40mm 制定出如图 3.4 工艺方案。
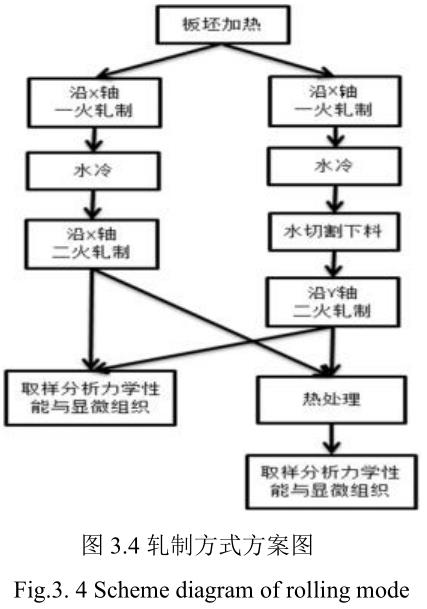
实验方案:
工艺 A:熔炼→锻造→板坯加热(单相区)→热轧(沿 X 轴)至 90mm→水冷→二火加热(两相区)→热轧(沿 X 轴)42mm→热矫→表面处理(水磨)→热态取样→成品热处理取样分析。
工艺 B:熔炼→锻造→板坯加热(单相区)→热轧(沿 X 轴)至 90mm→水冷→切宽 1040mm(中断)→二火加热(两相区)→热轧(沿 Y 轴)42mm→热矫→表面处理(水磨)→热态取样→成品热处理取样分析。
3.1 轧制方式对TC11钛合金厚板显微组织的影响
将两种工艺方案的不同方向变形量列表 3.5 如下:

轧制到 40mm 板材后板材的热态显微组织如图 3.5 所示,退火态下的纵横向显微组织如图 3.6 所示。

由图 3.5 可以看出,热态的两种工艺下,组织均为由少量等轴的α相和拉长呈编织状的α相以及残余β相组成的网篮组织。图 3.5(a)横向组织由于此方向一直未发生形变,因此等轴的α相比例稍高。但是从纵向 3.5(b)中可以看出此方向晶粒明显被拉长,在高温变形过程中,发生动态回复再结晶,新生成的α相明显有拉长并沿伸长的β晶界处富集。此时的位错能相对较高。从形貌上看,新生成的拉长的α晶粒纵横比一般为 10~20。而图 3.5(c)可以明显看出晶粒尺寸大于图(a),这是由于板材在横向上先发生大量变形,在变形过程中更早的发生动态回复与再结晶,优先生成的再结晶晶核长大时间较长,长大更为充分所致,从图纸形貌上观察纵横比约为 7~10。图 3.5(d)为工艺 B 的热态纵向显微组织,从图中可以发现其晶粒尺寸稍大于全横向轧制工艺。但是新生成的拉长的α晶粒纵横比略小于工艺 A,同时β相比例稍高于工艺 A。这是由于纵向累积变形量小于 A工艺所致。尤其在二火轧制过程中,工艺 A 虽然纵向总变形量为 80%,但是先发生接近 50%的变形量,并充分冷却后再发生 57%左右的变形量。这对式样的纵向拉伸性能影响十分巨大。
两 种 轧 制 工 艺 下 获 得 的 热 态 板 材 进行 热 处 理, 热 处 理制 度 为 990 ℃/1hAC+550℃/6h FC,退火后显微组织如图 3.6 所示。

从图 3.6 中我们可以看出,两种工艺下的板材经成品退火后,初生α晶粒逐渐断裂开来(等轴化),次生α晶粒条状化,呈双态组织,并且晶粒有长大趋势。
同时其显微组织与原始初生α晶粒的形貌息息相关。两种工艺的显微组织也有明显区别,A 工艺板材经退火后,初生α晶粒比例略低于 B 工艺,同时随着固溶时效退火的进行,初生α晶粒比例低于热态组织,残余β晶粒与次生α晶粒交错形成在原始β晶界处。工艺 B 板材经高温退火后,α相向β相转变,且编织状的长条α逐渐等轴化,在后续时效过程中,β基体中析出次生α,呈条状分布。同时可以明显的看出工艺 B 的纵横向显微组织差异更小。
3.2 轧制方式对TC11钛合金厚板力学性能的影响
为研究不同的轧制方式对TC11钛合金厚板性能的影响,对不同轧制工艺下制得的热态板材的纵、横向室温拉伸和冲击性能进行了测试。表 3.6 为经两种不同轧制工艺轧至 40mm 时热轧板的纵、横向力学性能。

对两种轧制工艺下获得的热态板材进行热处理,热处理制度为 990℃/1hAC+550℃/6h FC,对其纵、横向室温拉伸和冲击性能进行了测试。表 3.7 为经两种不同轧制工艺,两火轧至 40mm 后,经 960℃/1h AC+550℃/6h FC 双重退火后的力学性能。

从表 3.6 和 3.7 中可以看出,工艺 A 由于两火次变形均沿一个方向发生形变,导致力学性能差异巨大,各项异性明显。纵横向力学性能差值近 70MPa。而工艺B 由于两个方向均存在较大程度的变形各向异性减弱,纵横向力学性能差值为20MPa 左右。工艺 A 的横向力学性能较差,但是工艺 A 的 L 向力学性能较为优异,延伸率也较好。这与纵横向变形不均匀有直接关系。退火前后工艺 B 的冲击性能均高于工艺 A,A 延伸率也优于工艺 B,从显微组织可以明显看出,由于工艺 A 的组织更为等轴化,工艺 B 片层状的晶粒以及退火后生成的片层状的次生α晶粒相对冲击裂纹的扩展起到阻碍以及改变路径增加了吸收的能量。因此在退火后对材料的冲击性能均有较大幅度的改善。
4、 开坯变形量对TC11钛合金厚板组织及性能影响
为了研究不同的轧制变形量对TC11钛合金厚板组织和性能的影响,本文选用表 3.1 中 2#工艺(β单相区开坯),并采用了三种不同的轧制变形量对TC11板材进行开坯轧制。表 3.8 为不同轧制变形量的轧制工艺。
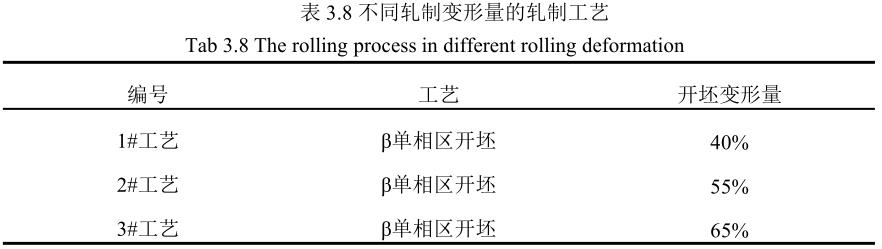
对三种不同的轧制变形量工艺制得的 40mm 厚TC11板材,分别测试其热态的显微组织及力学性能,并进行对比,研究不同的轧制变形量对TC11厚板热态显微组织的影响,随后对该三种工艺下制得的板材进行 990℃/1h AC+550℃/6h FC成品热处理,对比分析三种工艺对成品TC11板材的组织及性能的影响。
4.1 开坯变形量对TC11钛合金厚板显微组织的影响
为研究不同的轧制变形量对TC11钛合金厚板热态显微组织的影响,对不同轧制变形量的工艺下制得的热态板材进行显微组织进行了观察。图 3.7 为相同TC11 坯料经三种不同轧制变形量轧制到 40mm 时热轧板的显微组织。
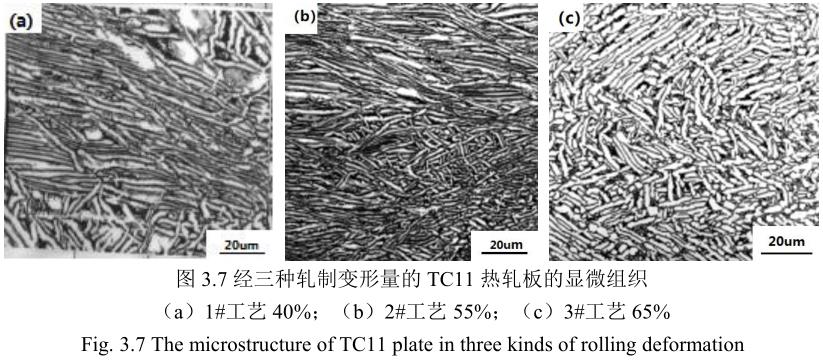
从图中我们可以看出不同的开坯变形量对成品板材热态组织影响很大。当开坯变形量为 40%时,板材获得长条α和局部网篮组织,当开坯变形量增大至 55%时,形成不均匀的网篮组织,此时长条α仍较多,而当开坯变形量继续增大至 65%时,板材获得了均匀的编织状网篮组织。这是由于变形量较小时,晶粒内部的α束集未完全发生变形,随着变形量增大,长条α发生扭曲变形,不同方向的长条α相互交错,呈编织状态,因此网篮组织越均匀。所以,在单相区加热并开始轧制,同时开坯轧制时变形量控制在 60%左右时,板材可获得均匀的网篮组织。
对三种轧制工艺下获得的热态板材进行热处理,热处理制度为 990℃/1hAC+550℃/6h FC,对其显微组织进行了观察。图 3.8 为经三种不同轧制工艺,两火轧至 40mm 后,经 990℃/1h AC+550℃/6h FC 双重退火后的显微组织。
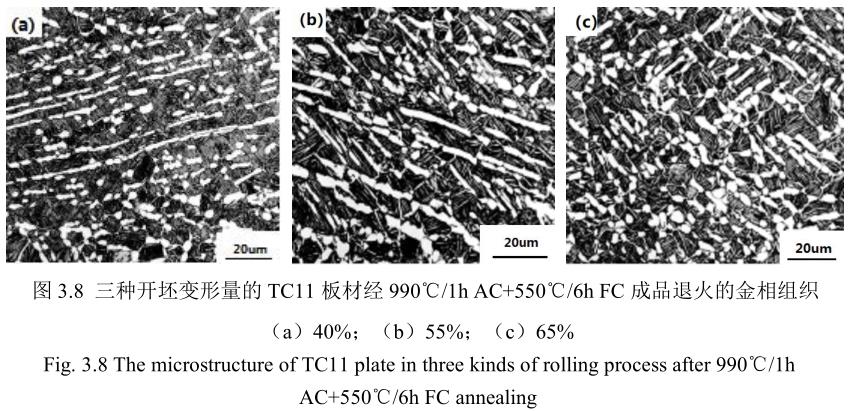
从图中我们不难看出,三种轧制工艺下获得的板材经成品双重退火后均得到双态组织。但开坯变形量为 40%的板材经退火后形成有大量长条α存在的双态组织,而当开坯变形量增大至 55%的板材经退火后获得了不均匀的双态组织,长条α仍然存在,当开坯变形量为 65%时,板材经退火后获得均匀的双态组织,晶粒尺寸细小。
对比TC11钛合金板材的热态和退火态组织发现,其组织有良好的传承性,均匀的网篮组织经双重退火后得到的双态组织非常均匀,晶粒尺寸细小。
4.2 开坯变形量对TC11钛合金厚板性能的影响
为研究不同的轧制变形量对TC11钛合金厚板性能的影响,对不同轧制变形量的工艺下制得的热态板材的纵、横向室温拉伸和冲击性能进行了测试。表 3.9为经三种不同轧制工艺轧至 40mm 时热轧板的纵、横向力学性能。
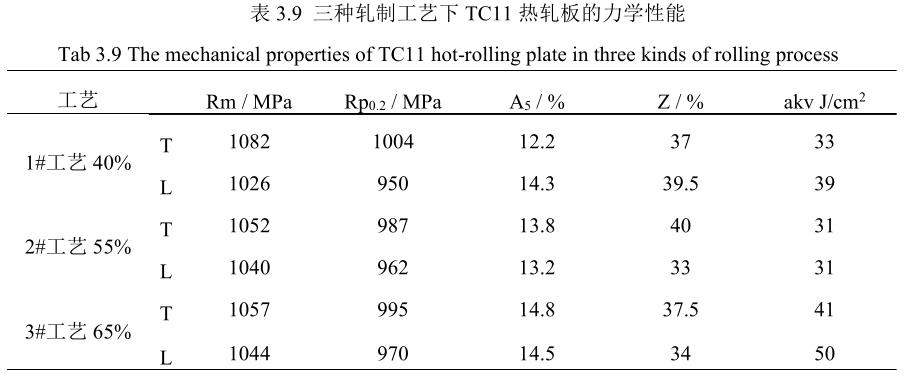
从表中可以看出:三种轧制工艺下,板材的抗拉强度均能达到 1020MPa 以上,延伸率达到 13%,冲击韧性大于 30 J/cm2 。随着开坯变形量的增加, TC11热态板材的纵、横向性能差异逐渐变小,这主要是由于网篮组织随着变形的增加而变形均匀;同时,随着开坯变形量的增加,TC11 板材热态冲击韧性逐渐提高,这是因为开坯变形量越大,板材获得更加均匀的网篮组织,编织状交错的α相有阻碍裂纹扩展的特性。
对三种轧制工艺下获得的热态板材进行热处理,热处理制度为 990℃/1hAC+550℃/6h FC,对其纵、横向室温拉伸和冲击性能进行了测试。表 3.10 为经三种不同轧制工艺,两火轧至 40mm 后,经 990℃/1h AC+550℃/6h FC 双重退火后的纵、横向力学性能。

从上表可以看出,经 990℃/1h AC+550℃/6h FC 双重退火后,三种工艺下的板材强度和冲击韧性有了大幅提升,塑性也有所提高。这是由于经退火后,网篮组织转变成了双态组织,大量的片层状次生α相,提高了材料的强度,也利于材料的冲击性能。且随着开坯变形量的增加,板材的纵、横向性能差异逐渐变小;同时,随着开坯变形量的增加,TC11 板材强度和冲击韧性逐渐提高,这是因为开坯变形量越大,板材获得更加均匀的网篮组织,经退火后获得细小的双态组织,细小的等轴组织有利于提高材料的强度,细小的片层状次生α有阻碍裂纹扩展的特性,从而提高板材的冲击性能。
由于本研究涉及企业的新产品开发技术,根据企业技术保密协议和订货商合同要求,研究中的部分工艺参数不能详细表述,仅做相关原则说明。
4.3 开坯变形量对TC11钛合金厚板不同厚度位置显微组织的影响
由于设备能力有限,热轧厚板在开坯轧制过程中的实际单道次压下量有限,轧制过程的变形总是会从板坯的表层逐渐渗透到板材心部,为保证板材厚度方向上的组织一致性,必要保证材料的道次变形量和总变形量。但是实际工业生产过程中,由于在轧制过程中的温降,板坯表面和边部降温尤其快,随着温度的下降材料的塑性明显降低,这个时候如果继续大变形量变形会导致材料表面和边部开裂,使成品率下降,或产生废品。因此选择一个合适的经济实用的变形量对于厚板的工业化生产十分必要。图 3.9、3.10、3.11 分别反映开坯变形量为 40%、55%、65%变形量面材料表层与中心层的这种差异图。

上图为开坯 40%变形量下TC11中心层与表层的显微组织,为增大视野,更多的暴露出高向上的形变差异带来的组织差异,选用 200 倍显微组织图作为比对。可以在图 a 中间明显看见高向上未完全破碎的原始α晶粒。区间范围为中心层约 100~150μm。这种未破碎的拉长状组织纵横比一般为 0.1,甚至更多,这与上下表层发生变形后的长条状α晶粒纵横比一般为 7~20 呈现出巨大差异,为这会对材料的拉伸性能带来巨大影响。
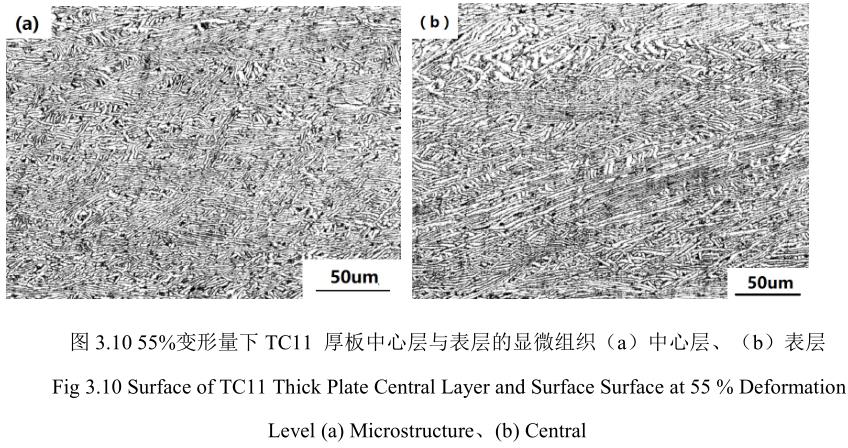
上图为开坯 55%变形量下TC11中心层与表层的显微组织,从上图中可以明显看出,在高度方向上,不同位置的板材均发生较好变形,晶粒破碎充分。初生的α晶粒呈略微拉长状态。并且纵横比总体小于图 3.9 中 40%变形量下的纵横比。
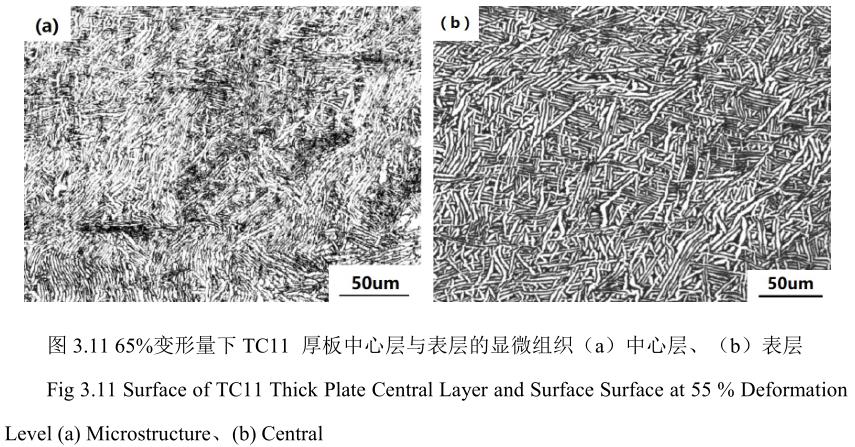
上图为开坯 65%变形量下TC11中心层与表层的显微组织,图 a 我们可以明显看出表层显微组织明显粗化,同时中心层局部地区出现出现β斑,这是由于变形量过大心部温度上升过快,使局部温度过高导致。适当的降低轧制速度可以有效改善局部过热现象。但是降低了轧制速度会导致材料表面及边部的温度大幅度下降,这在后续轧制过程中极易出现表面裂纹或裂边现象。如图 3.12 所示。

因此综上所述,TC11钛合金的开坯变形量最好控制在 55%~60%之间,变形量过小不利于变形深入到板材内部,而变形量太大轧制时间过长又容易出现板面裂纹和心部过热现象,如生产上必须采用更大的变形量时,适当降低轧制速度同时进行回炉再加热的方式进行轧制,由于具体轧制压下及回炉再加热工艺设计,涉及我公司TC11组织控制专有技术,本文不作相关描述。
相关链接